Beam & Block concrete flooring
For fast, low-cost, and robust construction, choose a Milbank precast concrete beam and block concrete floor. We have expertly manufactured precast concrete floor beams at our factory in Essex for over 75 years.
The UK’s leading manufacturer of Beam and Block flooring solutions
Benefits of concrete Beam & Block floor systems
UK-made pre-stressed concrete floor beams in 155mm or 225mm
Milbank precast beam and block concrete floor beams are expertly manufactured by our experienced operations team at our facility in Essex, UK, and are cast to a high-quality with excellent durability & longevity. We carry a permanent stock of over 25,000m of 155mm concrete floor beams, in varying lengths, to suit any order.
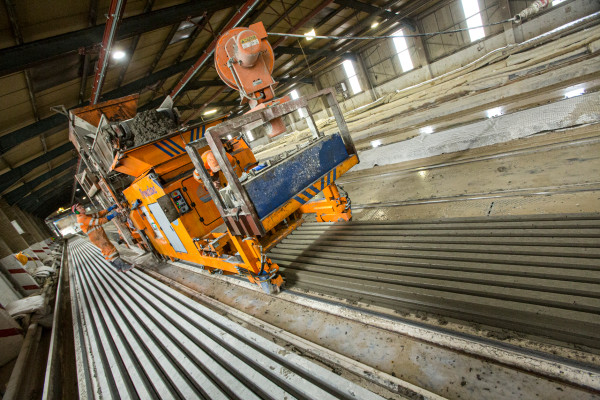
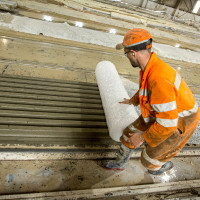
We also hold a limited stock of the thicker 225mm beams but are well equipped to efficiently manufacture concrete beams to order (in 50mm increments) up to 7.8m long. Our variability and flexibility, along with our dedication to providing exceptional levels of customer service, is what sets us apart from competitors.
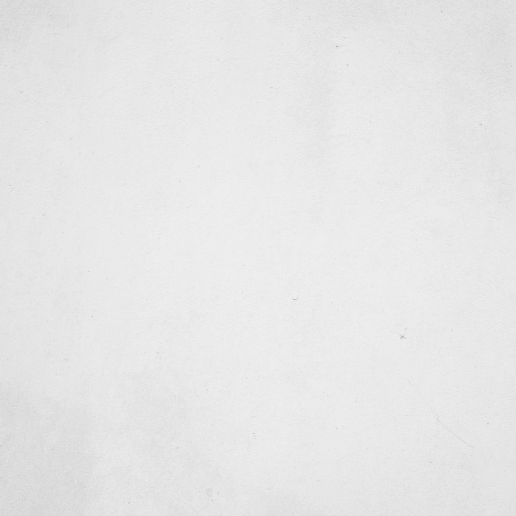
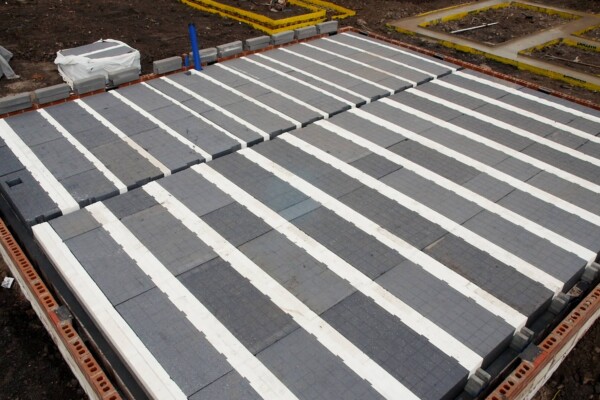
Milbank GDeck is a high-quality insulated alternative to a standard Beam and Block floor, combining high-performance expanded polystyrene (EPS) insulation with precision-engineered concrete components. With an integral structural top sheet, it reduces both installation time and on-site wastage, saving you time and money from the ground up.
Beam & Block FAQs
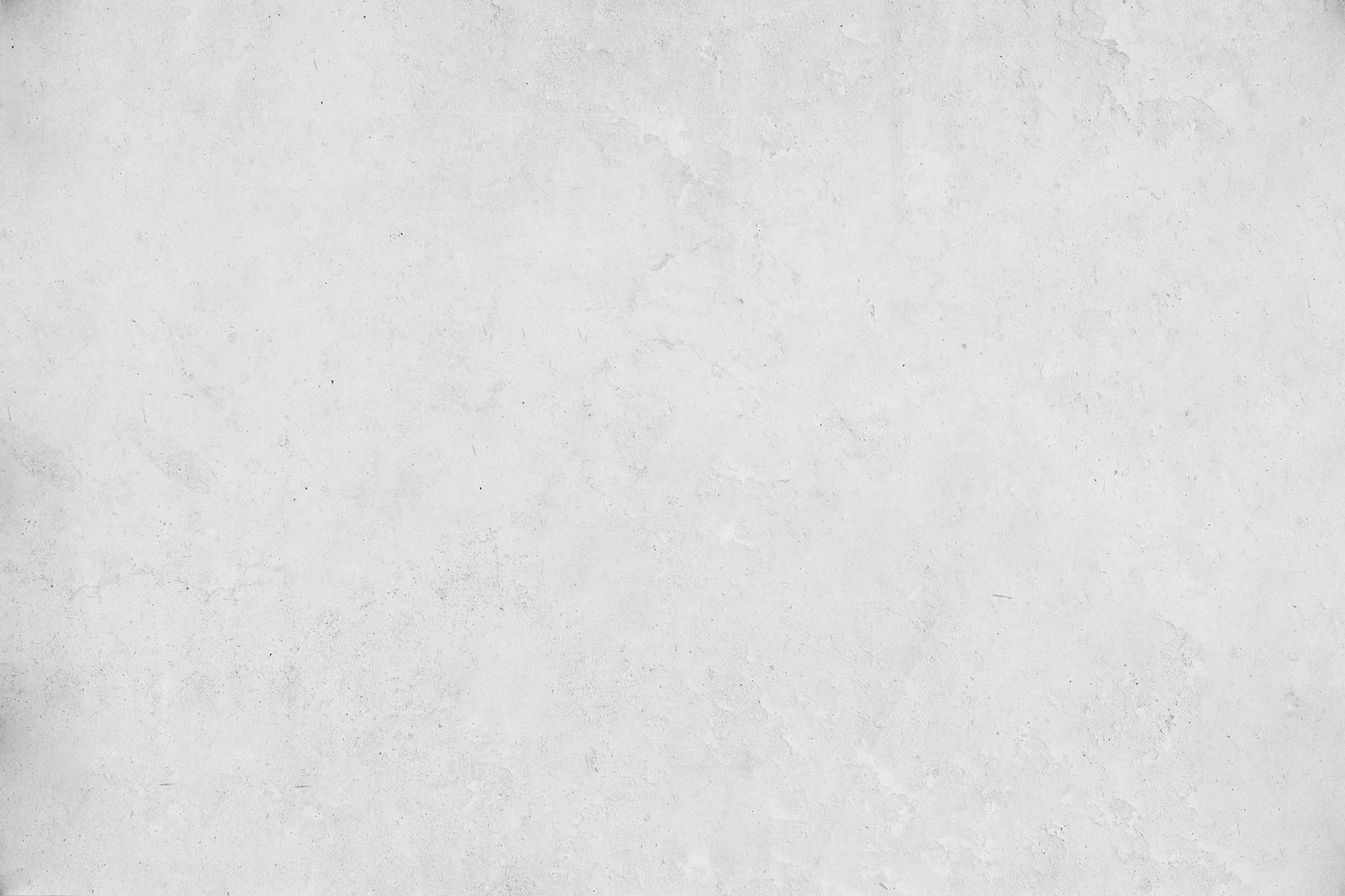
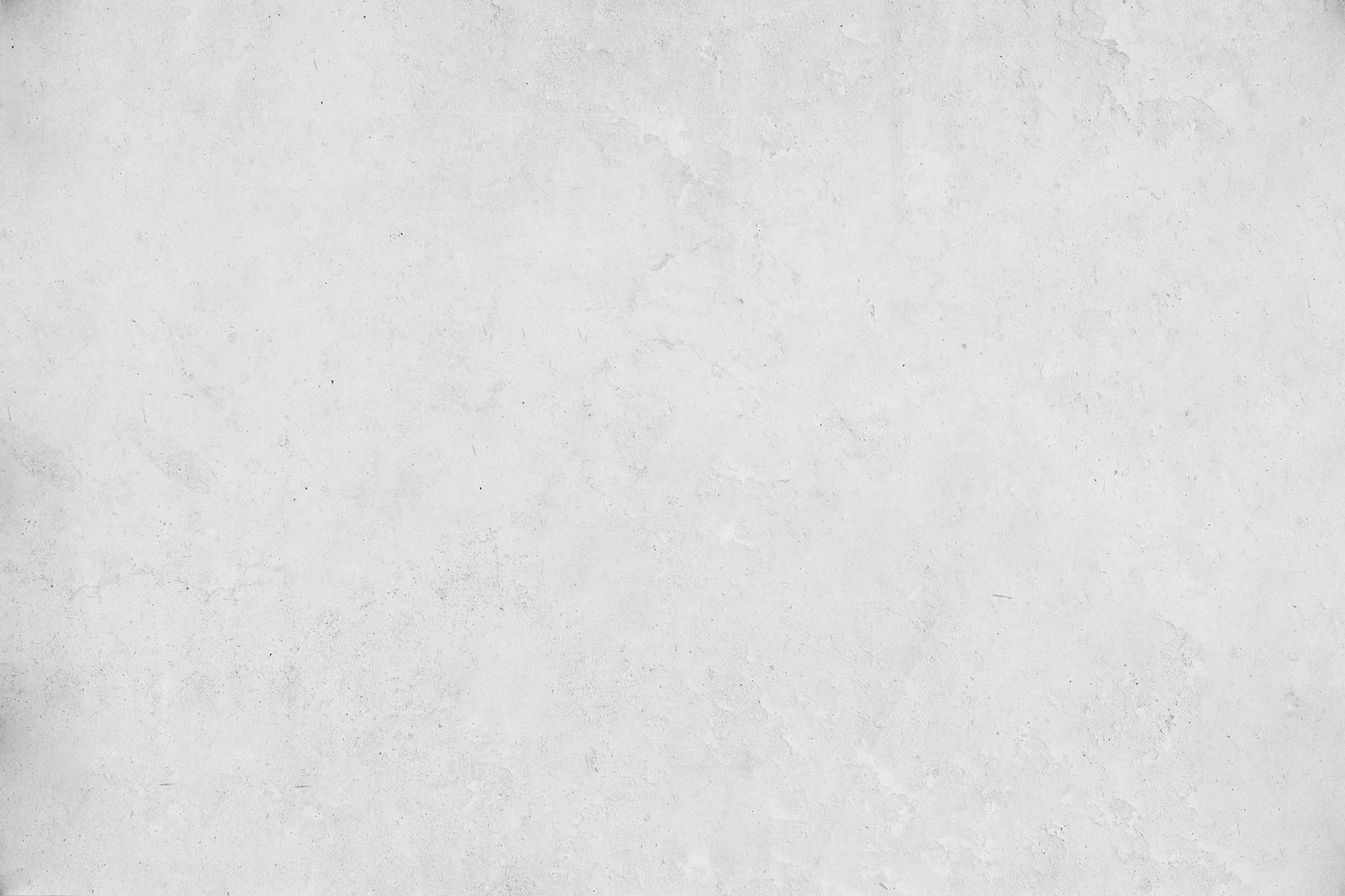
-
As the concrete products used are all precast at our factory, the installation is an entirely dry process. For this reason, the installation of beam and block is usually unaffected by cold or wet weather so can continue even during winter months.
-
The supporting blockwork needs to be laid first, but otherwise there is very little preparation needed. Minimal levels of excavation are required – with preparation at a minimum, project timelines are shortened.
-
The beams employed in these floors have a significantly longer span than timber & therefore it is much cheaper and easier to install than traditional timber methods.
-
Beam and block floors are maintenance free – completely unaffected by damp, rot, or vermin. These highly durable floors are clean, mould free, unparalleled in longevity, and are incredibly low cost over their lifespan.
Why choose Milbank as your Beam & Block floor supplier?
Milbank have been producing reinforced concrete flooring products since our origination in Chelmsford, Essex, in 1947. With over 75 years of experience manufacturing and supplying pre-stressed concrete beam and block flooring products, we’re confident that we can provide you with the perfect solution to your flooring requirements.
Our in-house team of industry-leading designers, manufacturing staff and installation gangs are continually driving our mission to deliver exceptional levels of service to our customers.
Mark Mullins
Silverstone Homes Ltd.
“We had Block and Beam installed yesterday and I wanted to draw your attention to what great workers Tom Roberts and his team were, and what a credit they are to Milbank’s workforce. They were polite, friendly, and nothing was a problem.
They marched on and got the job done; even when they thought they were going to get delayed they still all pushed on. I’ve had them on my last 2 sites and both times they’ve been brilliant. Please thank the boys for me.”
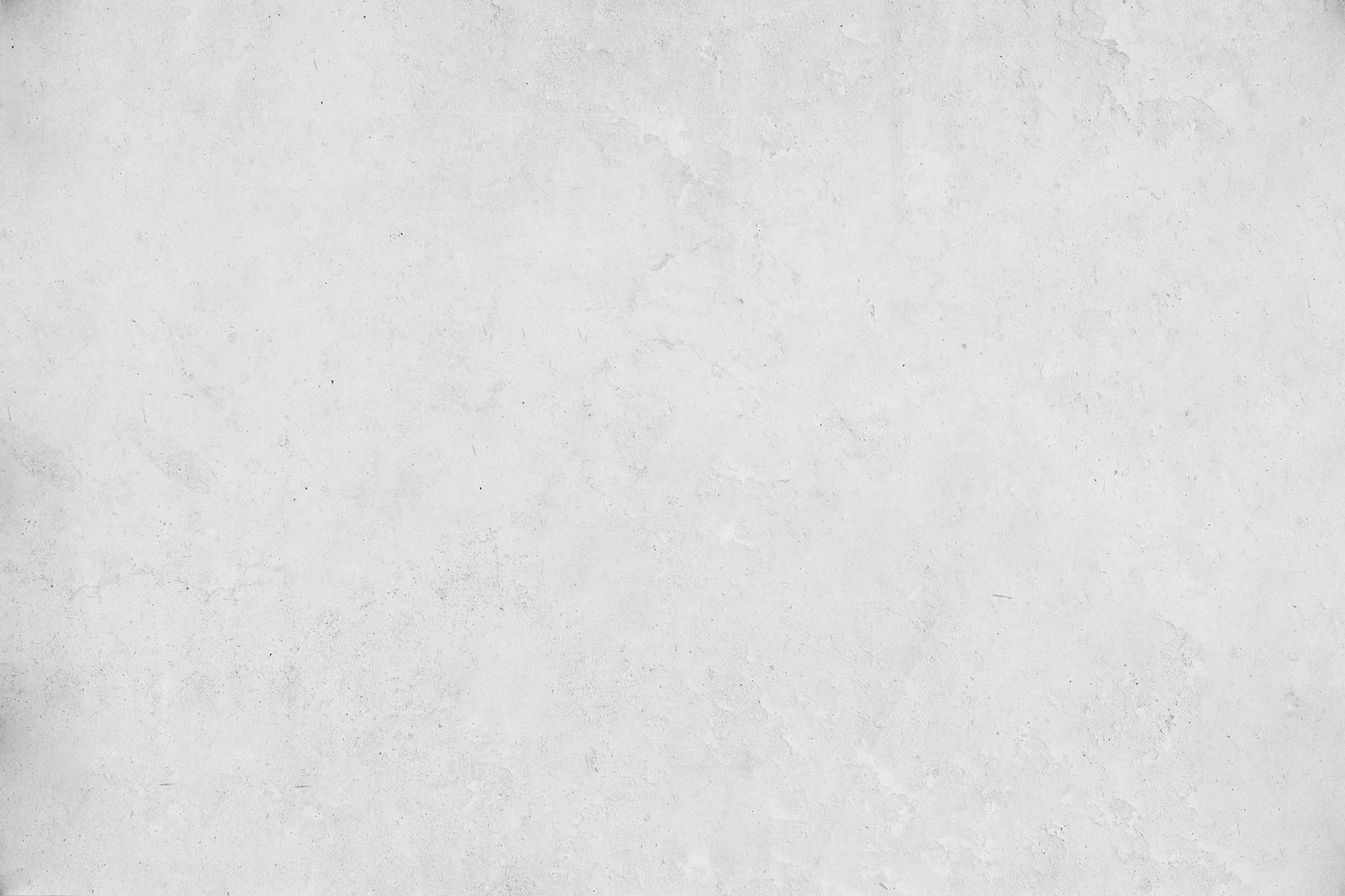
We are experts in Beam and Block floor installation
Our professional ‘all-in-one’ concrete floor service includes on-site installation, ensuring any issues are addressed quickly and efficiently from our head office. We cover all aspects of the design and installation process and pride ourselves on our quick response to queries, world-class manufacturing, and expert installation.
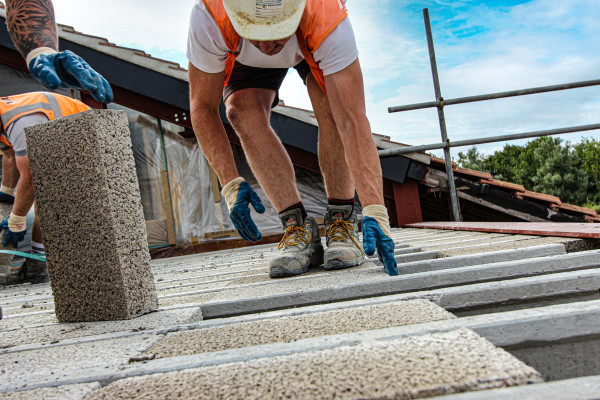
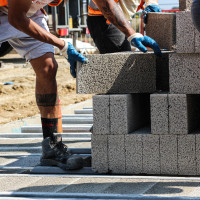
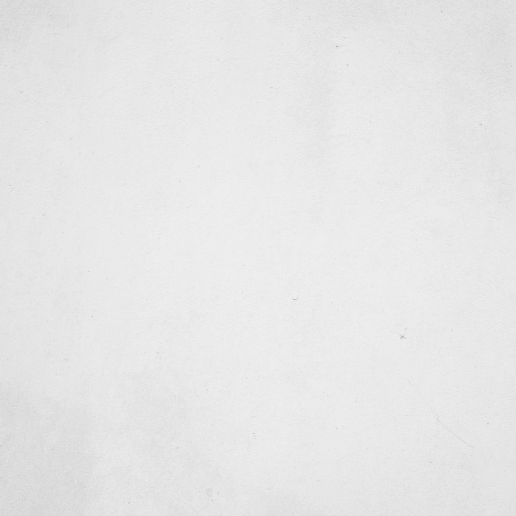
More reasons to choose Milbank for your precast concrete products
- We are environmentally conscious.
- Our installations are fully health and safety compliant, and we are stringent in our upholding of standards.
- Our staff have the experience and knowledge to help fulfil your project to the highest standards and on-time.
- We manufacture all our precast concrete products on site and install them to the highest standards.
- Use our Beam and Block Floorspan calculator to work out the size of floor space you will need.
- Look at our Load Span Tables.
- Download one of our data sheets for more in-depth information.
- Get in touch for a conversation, estimation, or just for advice.