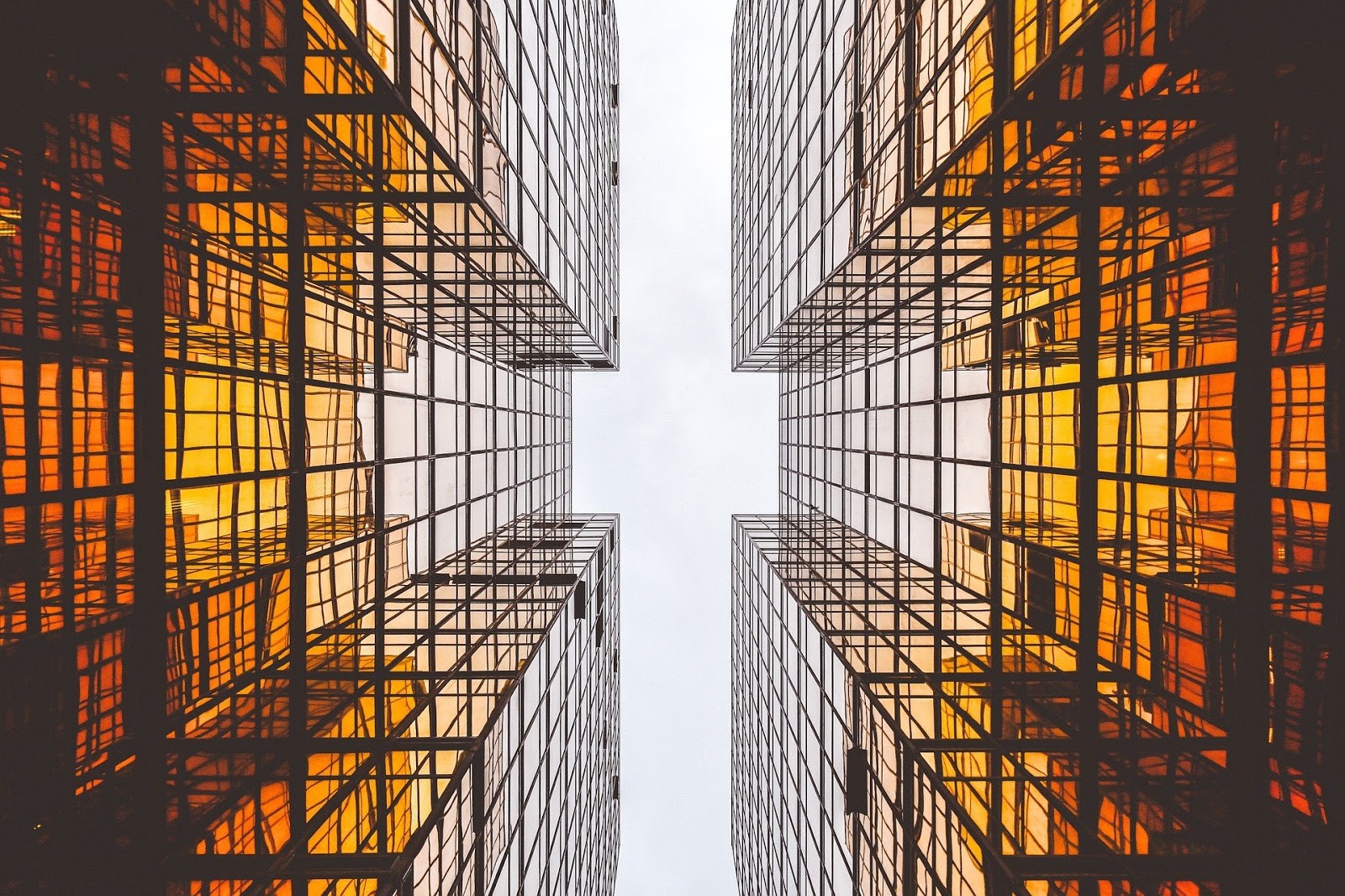
Why off-site offers quality, affordable, infrastructure for the future
With the construction sector being undeniably crucial to the government’s targets, whether they be economic or social goals, we must ensure that the future can provide quality and affordable infrastructure. Due to the demand for this infrastructure, housing, in particular, the sector must work towards modernising as quickly as possible. According to The Independent, we’re facing our biggest ever backlog of homes, a number around four million homes in-waiting has been proposed; we need to build 340,000 homes per year until 2031 to meet demand.
There is a way that the UK could be working better towards these targets, and that is further adoption of off-site construction techniques. Modular techniques, such as precast concrete products and other prefabricated sections, can be engineered off-site and then delivered. Despite monetary and time savings demonstrated by the method, the UK has been slow to embrace this technique – continually opting for the majority of construction to be carried out on-site. A survey undertaken by the Electrical Contractors Association demonstrated that 59 per cent of respondents stated a reduced operational cost when using off-site techniques. In addition, 57 per cent saw an increase in the quality of work and 61 per cent attributed these techniques to a rise in productivity. These figures, among other claims, show that the future must move towards off-site construction – especially when it comes to quality and affordable homes and infrastructure for our country.
Currently, only 7 per cent of UK construction is undertaken utilising modular construction. This behind Germany (9 per cent), Japan (12 per cent) and Sweden (20 per cent). When you consider that Japan is in a housing surplus, increasing our off-site commitment seems an excellent idea. The BRE innovation park has already shown us that a house constructed using these techniques can be built in a single day. Homes built offsite can be 30 per cent quicker, and at a 25 per cent reduced cost.
A Less Labour Intensive Construction Industry
The future of construction should be less labour intensive. This has the potential to be a monumental shift in the way people perceive the industry as a whole, as construction has been – and still is – synonymous with manual labour. The need for manual labour will always be present, but off-site’s capability to reduce this comes with significant cost impacts.
Modular construction allows designers to create and manufacture complex and intricate parts of builds. Atamate, in their article offsite construction: advantages in costs and efficiency, point out that these techniques will reduce the need for a series of differently skilled contractors. In addition, with the construction industry struggling to hire new, and experienced, workers – less labour is very much needed. The industry is going to have to find a way to deal with fewer workers, and the less-labour approach off-site offers could very easily be one of the resolutions to this.
With a less extensive need for labour, the industry can also make savings when it comes to accidents and ill health that are a result of continuous on-site work. Statistics revealed that this year 79,000 work-related ill health cases were reported (new or longstanding). This will be costing the industry a significant amount, and given a chance to reduce; it would only see construction as an overall more profitable sector. Needless to say, if the future was to embrace off-site techniques, these risks could be better mitigated.
A More Standardised and Simplified Process
Something that the “technological revolution” is bringing to every sector and business which it interacts with is streamlined and simplified processes. Where interconnectivity plays its part effectively, consistency and quality are more assured, and productivity inevitably arises.
Especially where time-bound project costs such as snagging* occur, off-site technology can very effectively eradicate these issues in the pre-build and build process. This will also reduce the work-life cost of assets due to impermeability and increased life-span. With processes organised effectively and accountability correctly assigned to each stage, an off-site construction project can come together fluidly accounting for future issues and specifications with the ability to prefabricate complex mechanical and engineering components.
A Profitable Export, Post-Brexit
In times of political unrest, especially surrounding Brexit, it is vital that the construction sector can quickly react to leaving the EU. Matthew Oakley, from WPI Economics, has looked extensively into how the construction should modernise in his report for Heathrow: The Value Of Off-site Construction To Uk Productivity And Growth. He believes that off-site production could provide a significant export opportunity for the UK post-Brexit. He points out that if we had increased this proportion to 25 per cent, we would have seen a 3.6 per cent increase in productivity by 2020.
This possibility of exporting prefabricated construction components would see the growth of the industry and the ability to share the UK’s great expertise with Europe and the wider world.
Another plus to utilise this method of construction is the fact the pre-constructed volumetric building units remove the dependence on centralised energy systems. The UK networking industry, among others in the world, are beginning to think forward to localised energy systems, in a bid to decrease carbon footprint and increase effective energy use. Olivia Gagan points out, in her article: moving towards a decentralised grid, that the UK is a long way from having a fully decentralised network. Some big UK companies are already seeing the benefits; M&S, for example, owns one of the largest solar rooftop plants in the UK. While we are not fully adopting this type of energy presently, the future will surely see more infrastructure move towards this type of energy and having it a possibility to be considered within off-site volumetric construction has the potential to be revolutionary.
So, For High Quality, Affordable, Infrastructure, the Future is Off-Site?
It would be ignorant to assume that this method is altogether faultless, else surely we would have already fully embraced it. At present, there are limitations within off-site construction. These limitations revolve around size. While prefabrication cuts out a lot of difficulties in the construction phase, due to transportation limitations, it may not be possible to prefabricate components of excessive size.
In addition, a machine will never be able to match the innovation of the human mind. Designers and engineers may find the current form of volumetric design constrictive in its modular limitations. One way to think about it is working with Lego – you must work within the constraints that the blocks allow.
As to be expected, the need for high investment in technology and training can be a real barrier to businesses embracing this type of technology. Although we see increased investment, there is still not yet enough to see off-site challenging traditional on-site methods.
However, as technology continues to develop, and new techniques of construction evolve, it is beyond doubt that off-site will play a part. With such a high demand for quality infrastructure, in a short period, we have no doubt the future lies in this method.
*snagging = checking building works before they finish and compiling a list of outstanding or unsatisfactory works to be completed.